sheet metal punch process Sheet metal punching is the process of creating holes and shapes in sheet metal using a punch and die. Readers will learn about the process, equipment, materials, optimization, quality control, applications, and future . For most applications, metallic enclosures for Wi-Fi components have proven ineffective unless there is an external antenna.
0 · square hole punch sheet metal
1 · slot hole punch size list
2 · sheet metal punch dies
3 · sheet metal hole punch press
4 · sheet metal hole punch machine
5 · rectangular sheet metal punch
6 · punching square holes in metal
7 · perforating operation in sheet metal
We tested 19 bread boxes to find the best ones for keeping loaves fresh for longer. Our favorite bread boxes can fit all kinds of baked goods and keep them from going stale for weeks.
Sheet metal punching is the process of creating holes in sheet metal using a punch press or a CNC punching machine. The process involves cutting and piercing the sheet metal using dies mounted on presses. Sheet metal punching is a cost-effective and accurate process for creating holes and shapes in sheet metal components. By following a guide, implementing quality control, addressing challenges, and ensuring safety, . Sheet metal punching is the process of creating holes and shapes in sheet metal using a punch and die. Readers will learn about the process, equipment, materials, optimization, quality control, applications, and future . Sheet metal punching is a manufacturing process used to create holes or shapes in metal sheets or plates with the help of a punch press. In this technique, a punch—a stiff metal .
square hole punch sheet metal
slot hole punch size list
Sheet metal punching, or subtractive manufacturing, creates holes, slots, or shapes by applying a mechanical punch through sheet metal. The force, usually made of hardened tool steel and pierces through the metal, removes the .Sheet metal punching refers to a metalworking process that entails forming holes in a metal workpiece. On the other hand, sheet metal blanking is a process of metal fabrication whereby the final product is eliminated from the larger metal.
In this comprehensive guide, we will demystify the sheet metal punching process, providing insights into its benefits, applications, and best practices. We will explore the equipment and tools required, discuss the .
Find out the best ISO correct sheet metal hole punches to give you the best precision and efficiency in your metalworking projects. Order Yours Today. . The draw stud plays a key role in any sheet metal punching process, as it is the part that attaches to the punch and dies, and applys the force to push the punch directly through the metal. .
This sheet metal forming process is often used for vehicle body parts, enclosures, and electrical components. It can be performed on most compatible sheet metal forming materials, like stainless steel, brass, . For this example, we will use 0.3752 in. as the shave-punch diameter. Fig. 1 depicts the next steps to determine the die-matrix and punched-hole diameters: The die-matrix opening should measure 1.25 to 1.50 percent . Punching machines, or punch presses, are powerful and versatile machines used in various industries. These machines utilize a mechanical process to create holes or shapes in metal sheets. Using punches and dies, they remove material from the sheet to achieve the desired outcome.
Punch force is the amount of force required to create a hole or cut in a sheet metal workpiece. It is a crucial parameter in sheet metal fabrication processes, particularly in punching operations. The punch force depends on several factors, including the material properties, thickness of the sheet, and the shape and size of the desired hole or cut.
Male die (punch/post) Metal sheet Blank holder (ring) on cushion Compressible cushion Sheet metal stamping/drawing – car industry •90million cars and commercial vehicles produced worldwide in 2014 Today’s sheet metal fabrication software systems pack powerful automated processing capabilities, including punch-sequencing macros and automatic tool selection. As a result, many shops lean heavily on the software, relying on built-in capabilities to provide optimum production solutions.The actual deep drawing process involves pushing a sheet of ductile metal (the blank) into a die by a punch, which forms it into the desired shape. The deep draw forming process can be repeated in a series of operations (re-draws) to create complex, intricate shapes.. This basic procedure provides the foundation for various deep draw stamping techniques, each . Sheet metal hole punching is a common method to create a hole in a metal sheet. In real practice, the process of hole punching differs depending on the materials, thickness, and the required hole shape. . The user can rotate to select the desired size and then punch a hole. It’s a seamless process, ensuring speed without compromising on .
This enables the initial sizing of metal sheets with accuracy, a fundamental step in the fabrication process. Punch Presses: Punch presses are used to create holes, notches, and other shapes in sheet metal. They use a punch and die set to cut through the material. They are very flexible for creating custom designs in the metal. Punch presses . Sheet metal processes involve a variety of methods to cut thin metal sheets. Understanding Piercing, Punching, and Blanking What is Piercing? Piercing is a metal fabrication process that create precise holes in sheet metal. The punch penetrates the material to create an opening, but it doesn’t remove any metal.Controls allow individual automation solutions for diverse sheet metal punching applications – including the ability to punch, cluster punch, form, edge roll, rolling offset flanges, countersink, counterbore, emboss, louver, extrude, tap, hinge barrel punch form, deburr, part mark, etch, and cut blank extraction in the same process, for efficient, precise processing.
sheet metal punch dies
One of the most mature technologies in metal fabrication, punching is also one of the most misunderstood, perhaps because the process can ccomplish so much—punch myriad shapes, form, even bend flanges. Regardless, if a shop follows some basic strategies, it will be well on its way to better parts and greater throughput.
Punching is a metal fabricating process that removes a fragment slug from the metal piece on the application of punch. Whenever the punch enters the punching dye, the process leaves a hole at the metal surface. The punching process involves a hardened steel punch that forces itself through a metal sheet giving perforations. Turret presses are CNC controlled and punch very particular shapes or holes in metal sheets using punch tooling. The Basics of Sheet Metal Punching. Sheet metal punching starts with creating the CAM instructions from the customer’s drawings, which will then be used to guide the turret as it punches the part.
The Punch and Die Set: Heart of the Process The success of the sheet metal punching process depends largely on the design and quality of the punch and die set. These components come in various shapes and sizes to accommodate different types of punching operations. For example, a punch designed for piercing will have a pointed tip, while a .
Find your metal sheet punching machine easily amongst the 76 products from the leading brands (EUROMAC, Voortman, ALFRA GmbH, .) on DirectIndustry, the industry specialist for your professional purchases. . the punching process is . The wear state of the punch in sheet-metal stamping processes cannot be directly observed, necessitating the use of indirect methods to infer its condition.Chap 2 , sheet metal – p. 1 . • variables of the shearing process punch force . speed of the punch . lubrication . . Chap 2 , sheet metal – p. 4 • the maximum needed punch force can be calculated from the formula P = 0.7 (UTS) t L where UTS is the ultimate tensile strength of the sheet The process involves sandwiching a piece of sheet metal between a punch and a die. Although it’s relatively straightforward, there is one design tip that can help you get your punched sheet metal prototypes as quickly as possible: following the 3:1 rule.
Vukota Boljanovic, Ph.D., has nearly 50 years of experience in applied engineering in the aircraft and automotive industries, as well as academia.He has performed extensive research in manufacturing engineering, including the impact of design and modification on sheet metal dies, jigs and fixtures, and process selection, aircraft assembly, and inspection tool and . Sheet metal piercing using high quality piercing punches and oil. Learn how to improve tool life, increase productivity and solutions to common problems. . These are variations of the piercing operation. Technically the cutting process is similar, but the resulting product will be different. . The punch and die must be hardened and tempered .Flat blanking is the process of stamping out the perimeter of a product from sheet or coil material to produce more complex metal blanks. Blanking can also be performed with flat non-metallic sheet or coil material. Pull-down and breakage Blanking of parts by punch press requires a punch and die combination between which the material is fed. Sheet Metal Punching Mechanism. This process is also known as Sheet Metal Hole Punching because it makes different shapes of holes on the sheet. A punch tool exerts force in sheet metal so the intended portion is punched out and results in precise and clean holes or cutouts similar to Puch’s geometry.
Stretching is the sheet metal forming process where the punch which creates the part shape forces the sheet metal to thin since lock beads prevent metal flow inward from the flange area. In contrast with drawing, significant metal thinning occurs in stretching, especially in the biaxial tension mode. The biaxial increase in surface area reduces .In this process, the metal sheet is molded into the shape of a die. The sheet is pressed onto the die or vice-versa using a hydraulic or mechanical press. The sheet can be hot or cold as it varies according to the requirements. . A die block is pressed on the metal sheet by a hydraulic or manual press to punch the hole. The size and radius of . Bending is a metal forming process in which a force is applied to a piece of sheet metal, causing it to bend at an angle and form the desired shape. 7. Two common bending methods are: V-Bending Edge bending V-Bending: The sheet metal blank is bent between a Vshaped punch and die.
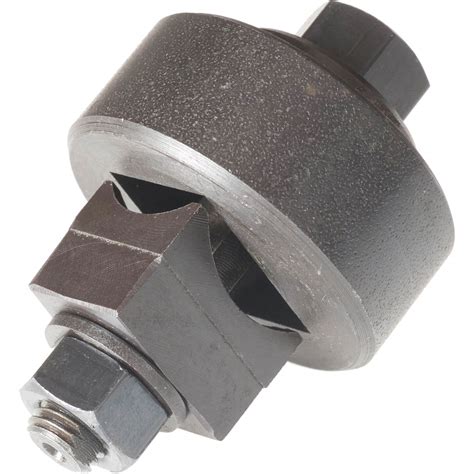
Metal roofs do not make a house hotter than other types of roof materials. Because metal roofs have a low thermal mass, they reflect light and heat rather than absorb it, like asphalt shingles.
sheet metal punch process|perforating operation in sheet metal